Felting machine needles are a crucial component of industrial felting machines, used for creating fabric and textile products through the process of felting. Felting is a method of matting, condensing, and pressing fibers together to create a dense, compact material. The needles used in felting machines are specially designed to efficiently and accurately pierce the fibers, entangle them, and bind them together to form a cohesive fabric.
These needles are typically made from high-quality steel or other durable metals to withstand the constant wear and tear of the felting process. They come in various shapes, sizes, and configurations, each designed to achieve specific felting effects and meet the requirements of different types of fibers and fabrics. Some common types of felting machine needles include triangular, star, and crown-shaped needles, each with its own unique properties and purposes.
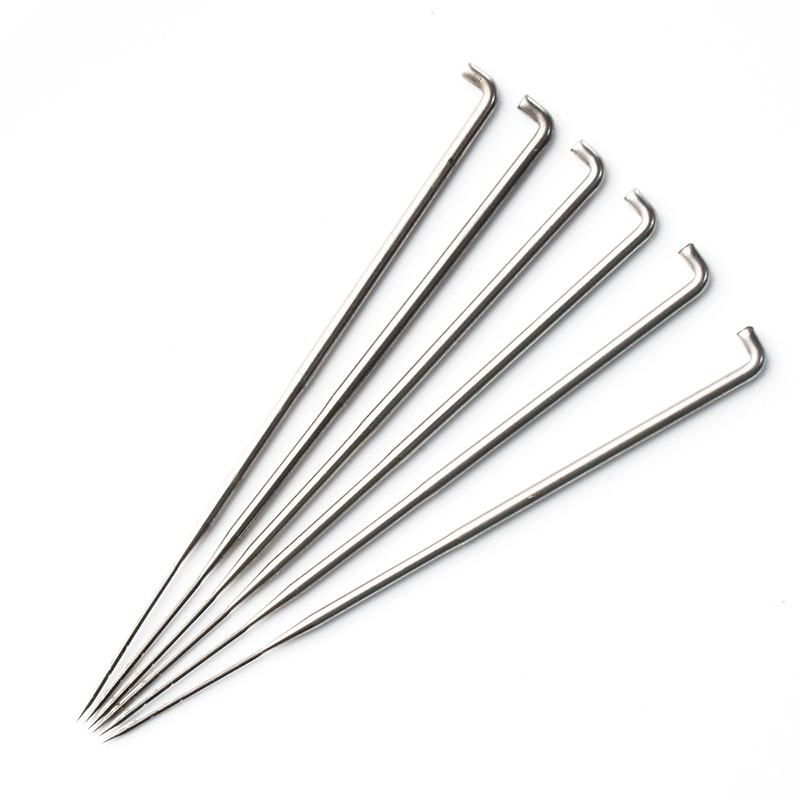
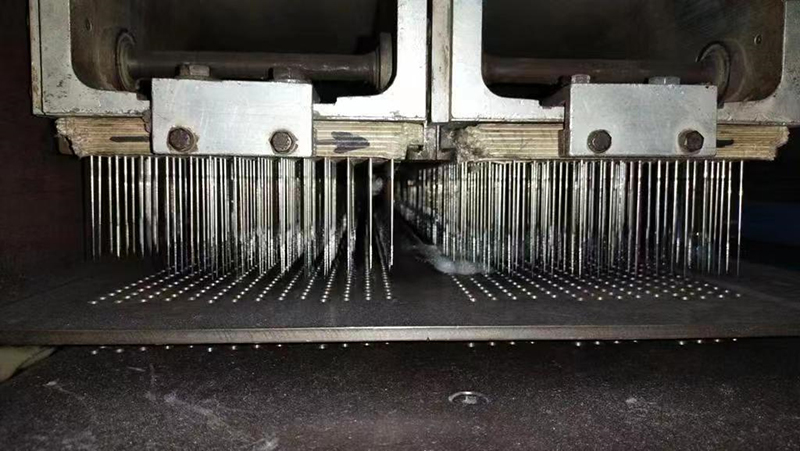
The design of felting machine needles is characterized by barbs or notches along their shaft, which are essential for catching and entangling the fibers as the needle penetrates the fabric layers. These barbs, often referred to as notches or burrs, are strategically positioned to maximize the entanglement of fibers and ensure the efficient matting process. Depending on the specific requirements of the felting application, the density and configuration of the barbs on the needle surface can vary.
In addition to the barbed needles, some felting machines also utilize special finishing needles that help smooth out the fabric surface and reduce the appearance of needle marks. These finishing needles typically have a different structure and barb configuration compared to the main felting needles, allowing them to achieve a smoother and more uniform texture on the fabric.
The selection of felting machine needles depends on various factors, including the type of fibers being processed, the desired fabric properties, and the specific requirements of the manufacturing process. For instance, finer needles with a higher gauge number are suitable for delicate or fine fibers, while coarser needles may be preferred for thicker and denser fabrics.
Furthermore, the spacing and arrangement of the needles on the machine's needle board or bed play a critical role in determining the overall felting performance and fabric quality. Proper needle density and alignment are essential for achieving uniform fiber entanglement and consistent fabric density across the entire fabric surface.
In industrial felting operations, the maintenance and replacement of felting machine needles are important aspects of ensuring consistent product quality and production efficiency. Over time, needles can wear out or become damaged due to the repetitive mechanical action and friction during the felting process. Regular inspection and timely replacement of worn or damaged needles are essential for preventing fabric defects and maintaining optimal felting performance.
In summary, felting machine needles are essential components of industrial felting machines, serving the crucial function of entangling and matting fibers to create dense, durable fabrics. These specialized needles are designed with barbs or notches to efficiently catch and interlock fibers, and they come in various shapes and configurations to accommodate different types of fibers and fabric requirements. Proper selection, maintenance, and replacement of felting machine needles are critical for achieving high-quality felted products and ensuring the smooth operation of felting machines in textile and fabric manufacturing processes.
Post time: Mar-09-2024