Industrial filter fabric needles are typically made from high-quality steel wire, as this material offers excellent durability and resistance to corrosion. The needles are designed to be strong and rigid, allowing them to penetrate and manipulate the layers of filter fabric during the manufacturing process without bending or breaking. The precise design and engineering of these needles are essential to ensure that they can effectively create the required openings and pathways within the fabric to facilitate efficient filtration.
The manufacturing process of industrial filter fabric needles involves several key steps. First, high-quality stainless steel wires are carefully selected and drawn through a series of dies to achieve the desired diameter and strength. The drawn wires are then cut to the required length to form the individual needles. Next, the needles are shaped and sharpened to ensure that they can effectively penetrate the layers of filter fabric without causing damage or distortion.
Once the needles are shaped and sharpened, they undergo a specialized heat treatment process to enhance their hardness and strength. This heat treatment process involves heating the needles to a specific temperature and then rapidly cooling them to achieve the desired metallurgical properties. The resulting needles are extremely durable and capable of withstanding the significant mechanical forces exerted during the filtration process.
The design of industrial filter fabric needles is tailored to the specific requirements of the filtration application. Different needle configurations, such as triangular, conical, or star-shaped, are used to create different types of perforations and channels within the filter fabric. The size, shape, and density of the perforations significantly impact the flow rate and particle retention efficiency of the filter fabric. Manufacturers carefully select the most suitable needle design based on the intended filtration performance and the characteristics of the particulate matter to be captured.
The proper selection and implementation of industrial filter fabric needles are critical to achieving optimum filtration performance. The needles must be precisely aligned and spaced to ensure uniform perforation and consistent flow patterns throughout the fabric. Additionally, the needle penetration depth and angle are carefully calibrated to create the desired pore structure while maintaining the integrity and strength of the fabric. These factors directly influence the overall effectiveness and service life of the filter fabric in its intended application.
In conclusion, industrial filter fabric needles are a fundamental component of filter fabric production, playing a vital role in the creation of the required pores and channels for efficient filtration. The careful selection of high-quality materials and the precise manufacturing process ensure that these needles possess the necessary strength, durability, and sharpness to penetrate and shape the filter fabric effectively. The design and configuration of the needles directly influence the filtration performance, making them a critical consideration in the development of high-performance filter fabrics for industrial applications.
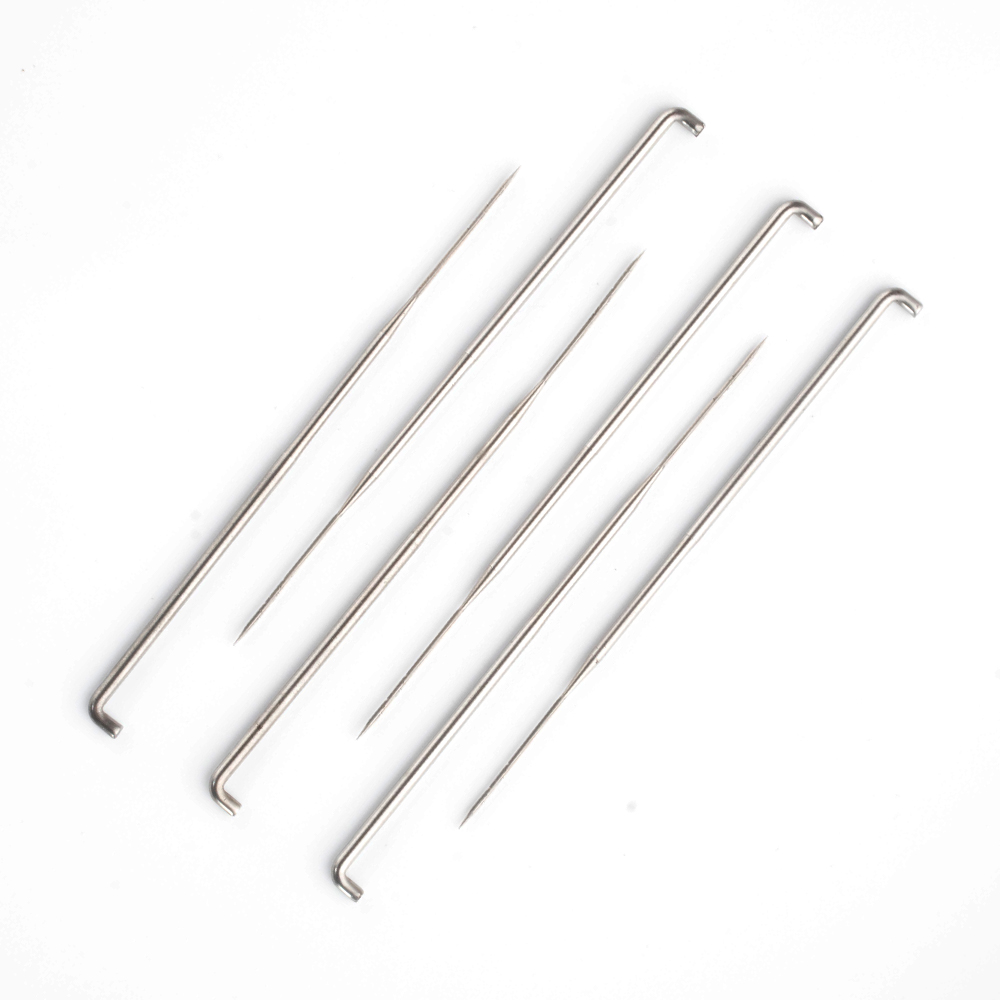
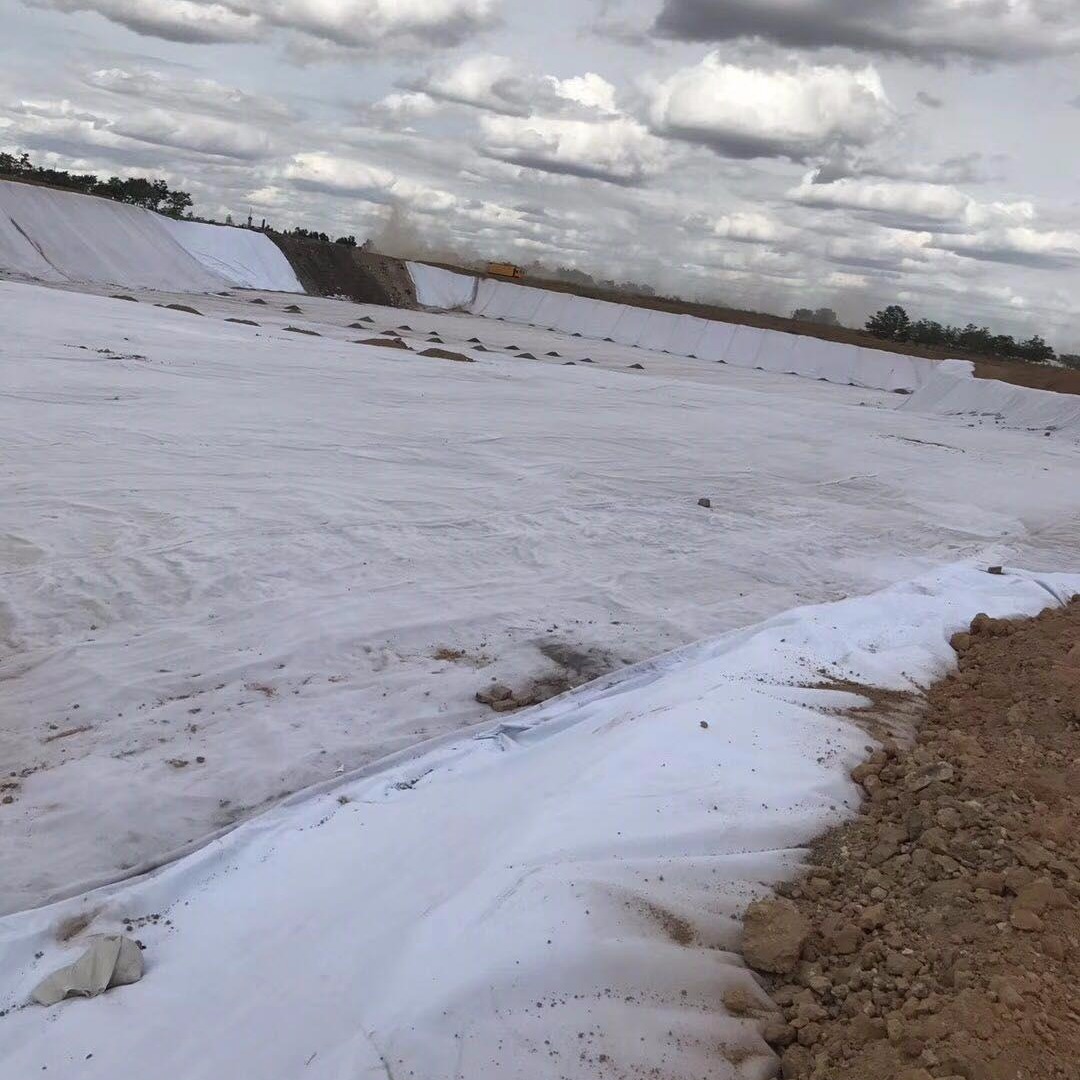
Post time: Jan-31-2024